With productivity in the homebuilding sector increasingly under the microscope and the need for rapid construction of new homes in Ontario recognized as urgent, it should be modular construction’s time to shine.
But several barriers remain stubbornly in the way of fully exploiting the solution says Albert Bendersky, vice-president of design with Hamilton-based manufacturer BECC Modular Solutions.
One is the lack of formal pre-approval or other recognition by the province and municipalities of proven standardized units, and another is a rigid building code that fails to take into account the new technologies.
BECC recently hosted a busload of planners on a tour of the firm’s facility as part of continuing outreach efforts to explain the finer points of modular construction to architects, planners and other construction stakeholders. The planners were in town for the annual Ontario Professional Planners Institute conference.
“We have to find those communication channels,” Bendersky told the planners.
“We can achieve the same results that have been achieved before,” he added in a later interview. “We can build any type of buildings. We can answer any type of municipal requirements, planning requirements, esthetic requirements, height requirements.
“It just a different way, different means, and it’s a new way. It’s the next level of technology you can use.”
The solution to the housing crisis, Bendersky said, is simple – it’s mass-producing top-quality buildings using the most sustainable time- and cost-efficient techniques with new technologies. The construction sector must learn to design, manufacture and install buildings using the advanced technological and industrial solutions of the 21st century the same way other industries produce cars and phones, he said.
BECC believes steel manufacturing is the way to go and the firm takes advantage of Hamilton’s high-quality steel, the architect said, but other modular firms effectively use wood or concrete.
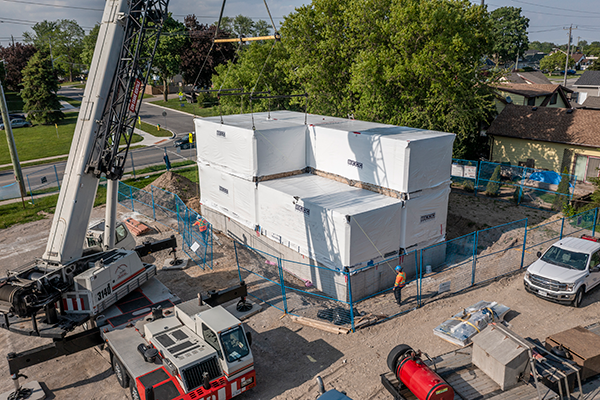
At the BECC plant, on a typical housing unit, the process starts with laser pre-cut, pre-drilled parts; crews assemble the module including pre-wiring and pre-piping, insulating, installation of mechanical, vapour barrier and cladding, drywall, finishes, flooring and windows; and the process is complete with the installation of appliances including toilets, furnishings and lighting.
BECC currently has a major project it is creating for a California client and the approvals process could not be more efficient, compared with Ontario, Bendersky said.
Explaining the permitting in general terms, he said that state has developed a system of design approval authorities, with private licensed engineers who represent the authorities and work with modular manufacturers. The engineer reviews drawings “in a very diligent way,” Bendersky explained, “then he issues comments and it goes back and forth.
“Then you get your building permit the moment it’s approved…Now, the moment it’s approved…I can build this unit anywhere in California without any (further) approvals.”
In Ontario, Bendersky said, there are layers of planning and politics. There is no pre-approval either at the provincial level, which would mirror California, or at the municipal level.
“If you have large municipalities like Toronto or Markham or Mississauga (pre-approving), that would be an achievement,” he said. “So that process of having some kind of pre-approval system that would allow maybe not every project, but most of the projects, or most typical projects, small projects…missing middle projects.”
Building inspections are not generally a roadblock, Bendersky said, but the gaps in the building codes are.
“The building code has to take into account that there are new technologies on the market, and those new technologies cannot blindly repeat certain details or certain requirements that have been in the building code for last 50 years. And it doesn’t mean that this new technology cannot achieve the same result.”
The construction schedule is 30- to 50-per-cent faster than linear and the sector is getting more sophisticated and “scientific,” using BIM platforms, AI tools and developing systems from purpose-built sub parts and sub-assemblies, Bendersky said.
BECC is planning an addition that will introduce more robotics, cutting the manufacturing time significantly. And Passive Haus and net-zero standards are achievable just as they are with traditional building.
Follow the author on X/Twitter @DonWall_DCN.
Recent Comments
comments for this post are closed