Ontario’s Ministry of Municipal Affairs and Housing on April 8 amendments to the Ontario Building Code allowing encapsulated Mass Timber °µÍø½ûÇøion (MTC) buildings up to 18 storeys. It opens up a number of interesting issues.
This proposal would put Ontario on par with the 2021 International Building Code (IBC) and see it join British Columbia and 28 U.S. states and jurisdictions that have adopted the IBC’s MTC provisions.
Under the IBC code, taller MTC buildings are permitted within strict guidelines regarding fire protection. These detailed provisions concern the “encapsulation†of exposed wood surfaces with cladding materials that deliver high levels of fire-resistance, based on the location of the MTC inside or on the exterior, and the size and height of the building; hence the term EMTC. Enhanced sprinkler protection is also mandatory.
Ontario’s announcement goes beyond the code amendment itself and speaks about potential benefits of MTC in terms of the province’s affordable housing shortage.
“The use of mass timber can help the sector build more homes faster, keep the cost of construction down and boost our northern economy,†said Housing Minister Paul Calandra.
Those are three bold statements.
Calandra conflates MTC construction with faster building. Second, by associating MTC with lower construction costs, he suggests housing affordability will improve. Thirdly, he claims expanded use of mass timber will be an economic boost for Ontario’s forestry industry. Each of these deserves examination.
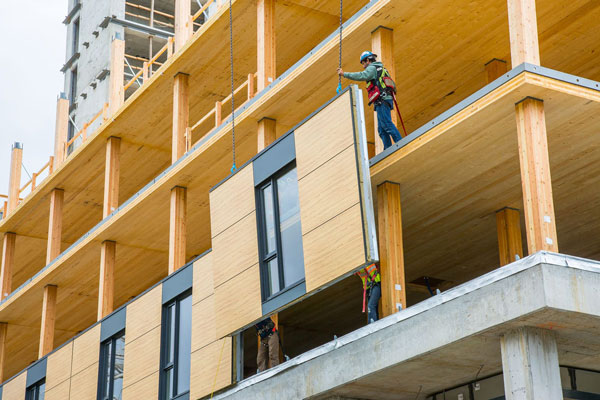
“Build more homes faster†has been the catch phrase of Ontario’s government ever since the housing shortage in Canada caught the attention of governments and the public. Does MTC answer that call?
Dan Lewis is director of mass timber and prefabrication at general contractor Skanska in Seattle, Wash. Writing for the an industry-supported organization promoting wood construction, Lewis makes the following statement: “Mass-timber assemblies can be constructed up to 20 per cent faster than concrete and steel assemblies.â€
Lewis writes that time savings can be realized largely through re-evaluation of project assembly schedules. Many relate to MTC prefabrication.
“Data shows prefabricated mass timber projects can increase efficiency in structural framing by 25 per cent and cut labour costs by 50 per cent, reducing overall project costs.â€
However, he adds it is difficult to quantify many other potential time savers, such as reduced trucking to site, smaller crews, less waste onsite, faster enclosure requirements, pre-co-ordinated MEPF penetrations, reduced dropped ceilings and more natural finishes.
In fact, Calandra’s statement speaks about, “a significant opportunity to shift housing construction offsite and into factories.â€
Industry reaction to this has been positive, although large-scale prefabrication or volumetric modular production in Ontario is currently limited. Significant investment in new facilities would need to take place.
Worth noting is the Ontario code announcement concerns EMTC for taller buildings. In housing terms, that means highrise residential. Whether more affordable housing will result for purchasers and renters is speculative.
A published by , another wood industry information resource, suggests rents and sale prices for multi-family units in large MTC buildings are significantly higher than “market standards.â€
Much of the premium is associated with the cachet of living in an MTC building. This casts doubt on Calandra’s hope for more affordable housing by using MTC in highrises. Faster to build? Potentially, yes. More affordable? Not sure.
Then there is Calandra’s assurance of a “boost†for Ontario’s northern economy.
Any increased production of MTC components has environmental implications founded in concerns over tree harvesting, an animated ongoing debate.
It boils down to the basic question regarding which is better: a mature tree standing in a forest; or a portion of that tree harvested, shipped out and then turned into building components, leaving the unused portion to rot or be burned, and a new seedling planted?
The worst outcome is rampant clear-cutting and a series of unmanaged forests, combined with the burning of wood scrap for heat or energy causing carbon
EMTC is more complex than first meets the eye.
John Bleasby is a Coldwater, Ont.-based freelance writer. Send comments and Climate and °µÍø½ûÇøion column ideas to editor@dailycommercialnews.com.
Recent Comments