Portland cement has been synonymous with construction for nearly two centuries. Despite the U.S. regionalism suggested by its name, the material in fact when U.K. inventor Joseph Aspdin patented the basic process of blending water with limestone from the Isle of Portland.
The Portland Cement Association (PCA) is considering a rebranding, including changing the name of the association itself. Last month, members were offered the opportunity to participate in a survey to share their “perspective on this important initiative.â€
Of concern to the PCA is the rise of blended concretes, many of which use recycled or more natural additives to reduce CO2 impacts on the environment. In contrast, Portland cement is associated with high GHG emissions.
“It is without doubt that PCA has had a significant past,†wrote Mike Ireland, president and CEO of the Portland Cement Association. “This exercise is to carefully consider our future.â€
However, Ireland adds Portland cement alone no longer adequately represents the increasing number of blended cement products PCA member companies manufacture.
There have been notable changes in processes related to the production of Portland and other cement and concrete products manufactured by PCA members. The PCA claims in its that 70 per cent of members now use alternate or renewable fuels in their production processes. Overall, 15 per cent of total energy use by PCA members comes from non-fossils fuels.
Much of the emissions from cement and concrete are traced to high production temperatures and chemical reactions that occur during the manufacturing process. These result in eight per cent of total global GHG emissions.
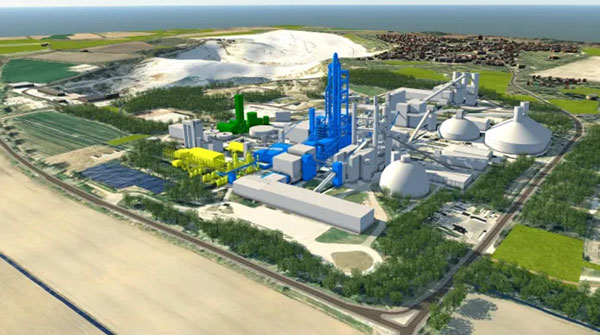
Across the entire industry, new carbon-reduced cement and concrete products are launched regularly. To further accelerate their adoption, an organization of manufacturers and developers has been created.
°Õ³ó±ðÌý(DC2), formed in January 2024, has 11 member companies sharing a mission of promoting the benefits of low-carbon cement and concrete, scaling up the industrial base for its production, and encouraging procurement of low-carbon cement and concrete to build future infrastructure.
“The coalition was formed in recognition of the crucial role played by the public sector, responsible for over 50 per cent of concrete purchases across federal, state and municipal agencies in the U.S.,†the group said in a “DC2 actively works to shape policies that will expedite the use of new low-carbon cement and concrete products in public infrastructure.â€
DC2 members are carving individual paths towards low-emission cement and concrete. Some now use electric kilns. Others employ a variety of carbon capture techniques to create additives that can be put back into the product to either replace or reduce the amount of limestone or Portland cement used.
It is not only smaller start-ups bringing new processing techniques forward. Some of the world’s largest producers are investing heavily in clinker-reduced concrete and cement products and other GHG reduction efforts.
For example, Swiss-based Holcim, the largest cement manufacturer outside of China, a 21 per cent reduction in its CO2 emissions per 2022 net sales, part of company-wide efforts to contain emissions.
“Sustainability accounts for two-thirds of the patent portfolio — 45 per cent directly relating to low-carbon solutions such as carbon capture and innovative low-emission raw materials,†the company said.
“Another 20 per cent are related to other sustainability drivers such as 3D printing, a great example of smart design that can reduce material use by up to 50 per cent.â€
“Holcim is decarbonizing construction at every stage of a building’s lifecycle,†writes Beat Hess, chairman of Holcim. “And because no single organization can do this alone, Holcim has been reaching out to all stakeholders who can help make construction more sustainable.â€
This includes partnering in studies around the world with over 40 leading universities, from materials science to civil engineering to sustainable construction.
More awareness of emission reduction developments can be expected from the DC2 and large industry players in the future.
John Bleasby is a Coldwater, Ont.-based freelance writer. Send comments and Inside Innovation column ideas to editor@dailycommercialnews.com.
Recent Comments
comments for this post are closed