A panel of off-site modular leaders at a recent agreed part of the solution to the affordable housing crisis in Canada is to manufacture houses in factories, but before that can happen there are many hurdles, especially at the municipal level.
The session, held at the University of Toronto’s Scarborough campus, was billed Off-site Modular ion Road Map, from Concept to Completion. It was moderated by Luke Dufour, a councillor for the City of Sault Ste. Marie.
“We build across the country and I can tell you that it’s crazy to me that we have different requirements in almost every municipality,” said Jackie Evans of.
“I know municipalities are trying really hard to hold onto control for some of that stuff, but it’s got to go because it doesn’t matter whether it’s modular or a standard developer, we need to be able to build at speed and at mass capacity. We don’t have time to mess around with every different municipality’s requirements.”
Unfortunately, Ontario is the hardest province to build in for modular builders and that needs to change, she added.
“We know how to build. Just let us build.”
Tendering and permits, a constant challenge
Getting building permits issued and the way municipal government tender for projects are two big challenges, said Patrick Chouinard of Element5, a mass timber manufacturer.
“Typically, they use a design-bid-build approach where municipal governments will hire an architect, who involves an engineer. They will design it and it will go to tender,” Chouinard explained. “That process can take a long period of time. By the time they design, engineer and go to tender with the building and then select the general contractor, they are already four to six months into it.”
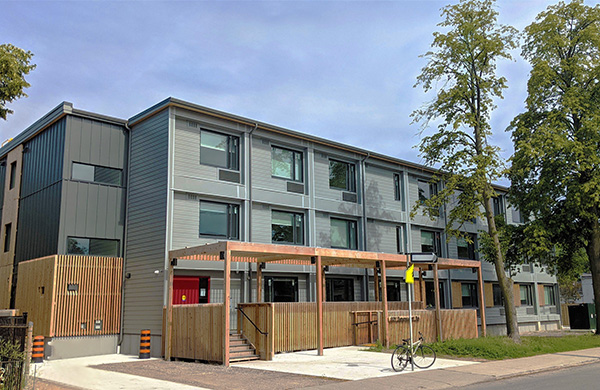
That usually results in going with a traditional build. A different approach is needed, he said.
“They say here’s a piece of property, here’s the amount of money that we have, this is what we’re expecting in terms of number of units and they go out to market. They get a number of organizations to put their own teams together to bid on them,” Chouinard said. “So, they’re getting light wood frame construction, volumetric modular, precast concrete, mass timber. It’s allowing the industry to come up with innovative solutions as to how to solve those problems. Municipal governments need to stop trying to figure out how to deliver modular housing and let the industry who understands this deliver this product.”
Standardization required around modular construction
Shailesh Poddar of , which builds tiny homes, said standardization is required.
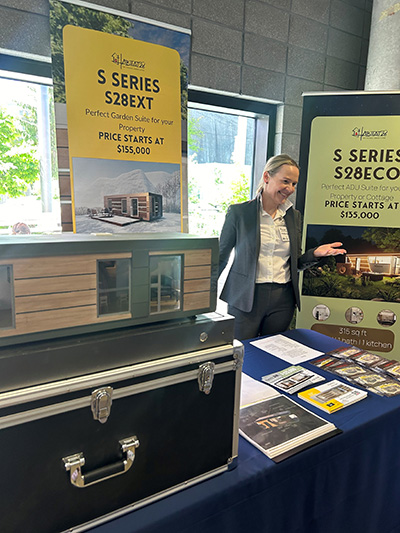
“If there was much more standardization norm, where every municipality had the same regulations that they are following, there would be a much larger consumer confidence in the product that is out there,” said Poddar.
“We need more houses being built in a factory where we can build it in two or three days and ship it out. However, we also need people to have that confidence to be able to live in them and buy them and use them for habitation. All of those things will happen when we have standardization.”
Eisa Lee of, a modular architecture firm, said standardization is also a dilemma for architects.
“We really need to look at up to what level do we standardize and be able to provide that guidance and provide the builders with a standing order in terms of OK, you guys will be able to build affordable housing buildings on these certain sites. We don’t know exactly what it’s going to look like but these are the volume of the project,” said Lee.
“If something like that can happen at the government level to be able to support the industry…that helps architects and engineers to prepare for that and be able to design for modular-ready or offsite-ready projects.”
Ontario has some ambitious housing targets and there isn’t enough capacity in the existing market to hit those deadlines, Chouinard noted.
“Investment is going to be required to invest to help subsidize other factories to increase capacity,” he said. “Even if we’re at full capacity we can produce maybe 80 buildings a year. That’s just scratching the surface of the need in the marketplace. So yes, it makes sense to move to modular construction. We hear a lot of talk about provincial funding, federal funding and I don’t see any of that invested in building infrastructure to help modular manufacturers move into the marketplace.”
Poddar said there is also a lack of education surrounding modular and off-site construction. For example, one GTA municipality took eight months to provide a permit.
“There is a certain amount of training and education that is required at the municipal level for municipal employees,” he pointed out. “Then there are other municipalities that look at this and say, ‘This is exactly what we need. This is how the problem is going to get sorted. What do you need from me to make this easier?’
“We need municipal employees to understand they are in crisis mode, we’re here to help them. Let us do our job.”
Follow the author on X/Twitter .
Recent Comments
comments for this post are closed